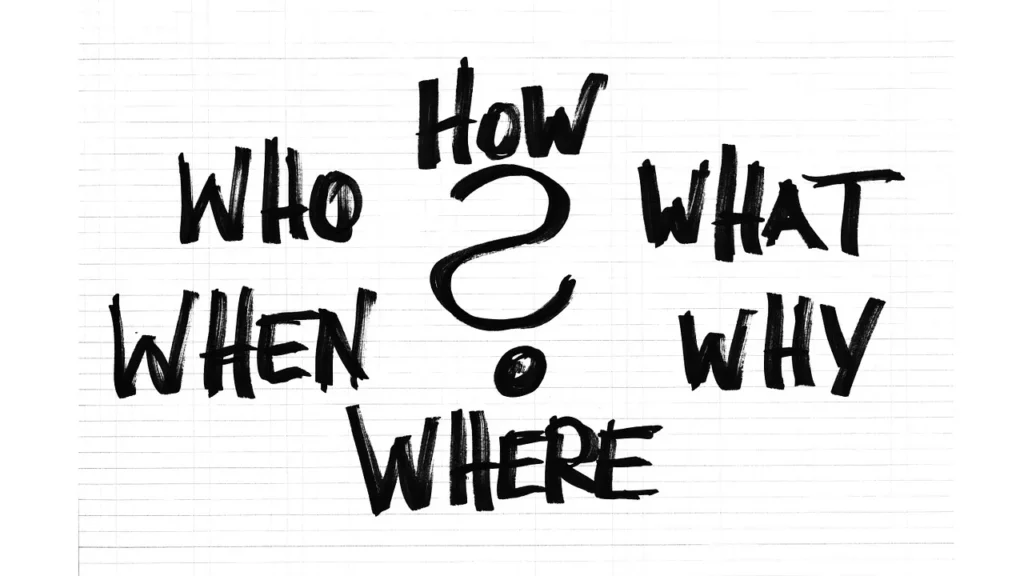
By David Calvert, 19th March 2024
We have previously made the case for a structured approach to “Design for Formulation” and in this post we look at some of the important terms used in the process.
The whole process starts with a “Customer Promise”, namely what your customer expects from the product and what you promise to deliver. It may seem blindingly obvious, but we have seen in many instances that, when pressed, companies find it difficult to express in a succinct way what they are going to deliver. Developments are often driven by an internal technology development or a vague perception of what the market needs. At its best the customer promise can be expressed in one, maybe two sentences.
From the “Customer Promise”, business and technical briefs will be developed. We will say more about those in the next article but these lead to definitions of what are the “Product Quality Attributes”. These are the properties of the final product that can be measured to determine that the product delivers on the “Customer Promise”. From these you start to define “Raw Material Attributes”, which are the properties of the raw material which are required to deliver the “Product Quality Attributes”. It is important to note that these are not necessarily measures you find on the raw material specification. As an example, the specification for the particle size of a powder may include a value for the D50, but you may find that the D10 or D90 are more relevant measures and could discuss this with your supplier.
The full list of these attributes may seem long and daunting and it is here that the “Risk Assessment” exercise is invaluable. This is not the typical risk assessment to decide whether a chemical is safe to use in the laboratory or in manufacturing but is an assessment of the consequences of what would happen to the product, and your promise, if you did not achieve the specific product or raw material attribute. Initially this assessment is based on “Prior Knowledge” (more of this in the next article) but as the process continues it is based on experimental or process data generated. By carrying out the risk assessment exercise, you develop an understanding of what is believed to be “Critical” and in your experiments you focus on quantifying this risk.
A similar exercise covers your formulation and manufacturing process and understanding the “Critical Process Parameters” which we will also cover in a future article.
In the next article, we will outline the five stages in the Design for Formulation process with a focus on the first stage “Getting Started” which is carried out before you even go into the lab.