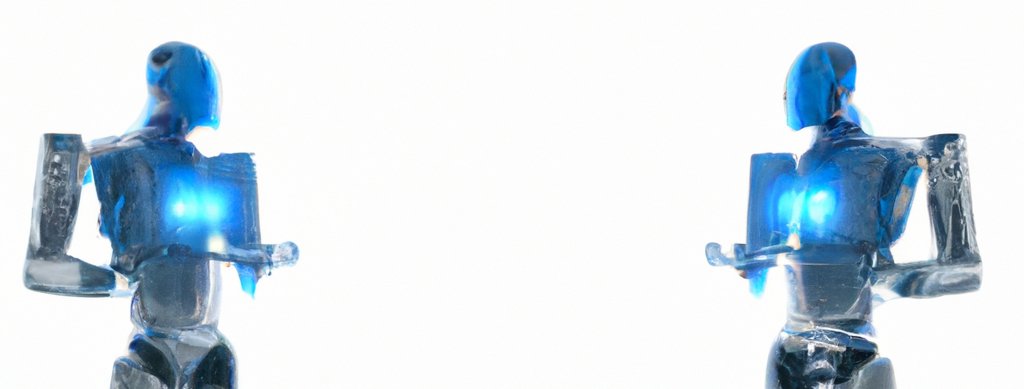
By Jim Bullock, December 2022
Formulations are complex systems with numerous variables. Quite apart from the numerous functional ingredients found in most formulations, a wide variety of different processing operations and conditions can be used when making formulations in order to achieve the desired product microstructure and the end performance. This all means that making changes in your formulation can have unexpected consequences. So, what happens if you want to make changes to an existing formulation and need to predict the impact of replacing a particular ingredient with another one, for instance on grounds of cost or environmental sustainability? Similarly, what happens if you have developed a formulation in the laboratory and would like to know how it would perform once scaled up to pilot or full manufacturing scale? The complexity of formulated products and formulation processes is such that this can conventionally be a tricky task.
Well, this is where a “digital twin” of your process could be invaluable. In the context of formulations, a digital twin is a digital simulation of, for instance, your product, your manufacturing process or your supply chain system. It can be used to help design products or processes, or to optimise them once they are up and running. In the latter case a digital twin can be furnished with real-time data from the process in order to help monitor and predict what happens if changes are made. Although the initial focus on digital twins might have been in the engineering sector, they are becoming more prominent in industries closer to home, such as pharmaceuticals and the food industry where processes such as fluid dynamics, heat transfer and mass transfer are modelled. Examples of digital twins in pharmaceutical manufacturing have been presented, and here the use of Process Analytical Technologies (PAT) to collect and report critical process and product data is a key component of the model. Moving on from production and into the use of formulated products, a digital twin of human skin has been developed and it is being used to predict the effect on the skin of cosmetic and pharmaceutical products, potentially reducing the need for animal testing.
Apart from optimising costs and performance of formulated products, digital twins can be used to predict the impact of changing processes from a sustainability point of view. So, in that context, it was interesting to see a real-life example reported in the recent Green Special edition of BBC Click (note that this may not be available to view in your country). In the programme, the consumer products company, Reckitt, explained how they had used a digital twin of their manufacturing and supply chain systems (developed by Risilience) in order to model the environmental impact of replacing an active ingredient in one of their headline disinfectant brands (Dettol®) with lactic acid. As well as the fact that it is derived from renewable raw materials, the use of lactic acid was found to reduce the overall carbon footprint of the product. A description of the Risilience collaboration with Reckitt on sustainable supply chains can be found on the Risilience website as well as in this video.
Formulated products and formulation processes have long been thought to be too complex for useful predictive models to be developed. However, as we have seen in these few examples, recent developments in sensing, measurement, scientific understanding, data processing and simulation – as embodied in the newest digital twins – have brought the dream of truly predictive formulation closer than ever to reality.
Image created by the author using DALL-E 2 AI art software.